The reasons for the failure are as follows: First, human factors, that is, insufficient attention to non-critical composite components, not in accordance with the regulations; second, the manufacturing quality of the parts themselves is unqualified, internal defects, or unreasonable design; third, environmental impact factors, Including fatigue, salt spray, sand, rain and snow, industrial waste gas pollution. In order to judge the defect failure of composite members, X-ray transillumination, C-scan ultrasound, acoustic emission and layered anatomy, laser holography, visual inspection, tapping and eddy current testing should be used.
Among them, the x-ray transillumination method and the C-scan ultrasonic method can provide the information and display position of the lateral crack of the substrate. The disadvantage is that it is sensitive to the directivity, the surface roughness affects the ultrasonic detection result; the acoustic emission can only detect the occurrence of the crack. The exact proof is also tested by layered anatomy and electron microscopy. Visual inspection is mainly carried out by visual inspection. The eddy current testing method is mainly used to detect internal defects. The laser holography method can diagnose both internal and external defects. The tapping method is to detect whether the sound is abnormal or not, and whether there is delamination and opening. Each of the above methods has limitations, and sometimes it can be used in combination with multiple methods.
Bolting and repairing with bolts, firstly remove the damaged part of the structure, drill the hole after bonding, and then fix it with bolts. The bolts of the metal reinforcing plate are bolted together, and the damaged part is first dug, and solidified with the sealing packing and the insert sleeve, and then The metal backing plate is fixed by bolts on the outside and bonded by a composite material patch.
During the production of highway painting, put glass bead into paint based on the ratio of 18-25% (weight percentage), so that the highway paint can still keep reflectivity during wear and friction. The ratio is refer to the specification of Communication Industry Standard of the People`s Republic of China No. JT/T280-2004, the standards which is different in different countries and areas.
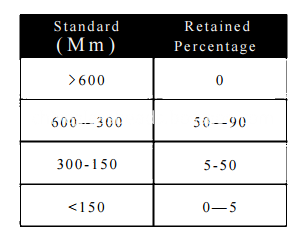
The appearance of glass bead should be colorless, loosen and spherical particle, should be clean without impurity, and without agglomeration |
According to the specification of Communication Industry Standard of the People`s Republic of China No.GB/T24722-2009, the granulometry is shown in the table below:
The glass bead can be produced based on the standard of countries or areas, such as EN1423/1424, AASHTO M247, BS6088, JIS R3301 and KS L2521 etc.
Intermix Glass Beads,Intermix Glass Beads Road Marking,Reflextive Intermix Glass Beads,Bicone Intermix Glass Beads
CHIYE GLASS BEAD (HEBEI) CO., LTD , https://www.chiyeglassbeads.com