More than a hundred years ago, people tried to make diamonds by artificial methods, but they have not been successful. The main reason is that it is impossible to build a container that can withstand 5~6GPa pressure and above 1000°C. It was not until 1954 that HT Haee et al. solved this problem that humans first synthesized diamonds. China's first "61" type ultra-high pressure high-temperature annual wheel mold was born at the end of 1962, which provides the most basic conditions for the experimental research of diamond synthesis process. It can be said that the two-sided anvil ultra-high pressure device has made a historic contribution to the rise of China's synthetic diamond industry. In 1964, the development competition for industrial production of diamonds was carried out in two kinds of devices (two-sided anvil and six-sided anvil device). The General Machinery Research Institute continued to vigorously develop large-scale “two-sided anvil†devices, which were successively in Changchun, Shanghai, Shenyang, Harbin and Xi'an. Cooperating to establish workshops and experimental bases, but after the development of technology is not mature, one of the important problems is that the carbide top hammer and pressure cylinder are too expensive. Later, the Institute of IOL established a research base for two-sided anvil devices. In the late 1960s, the diameter of the high-pressure chamber was Ø20mm, Ø32mm in the 70s, Ø40mm in the mid-80s, and Ø50mm in the 1990s. The Ø65mm cavity has been successfully developed, during which Ø32mm The cavity was very successful in the production and was promoted to the initial production in Wuhan, Wuxi, Changsha, Jilin and other places. However, with the maturity of the six-sided anvil device, the two-sided anvil devices were successively dismantled. In order to speed up the development of China's superhard material production technology, from 1979 to 1980, the Ministry of Geology Beijing Drilling Tools Factory and the Nuclear Industry Department 232 Factory successively introduced QRD-18 high-pressure synthesizing devices from Sweden and Finland. The high-pressure mold has a diameter of Ø40.5mm. The top anvil is Ø80.6×76.20mm, weighs 4.5kg, the pressure cylinder is Ø127×82.55mm, and the weight is 13.5kg. Both are imported from Sweden. The device generally reflects the production level of De Beers Co 1967~1969. After more than two years The use of the Ø40.5mm mold provided by Sweden shows good performance. It is worth noting that the cemented carbide used in high-pressure molds for synthetic diamonds in China is quite different from the world advanced level. The QRD-18 type device is taken as an example. Table 1 Domestic and international cemented carbide cylinders (inner diameter 40mm) quality comparison with foreign intermediate level synthesis process, the product is SDA series of high grade diamond, the average life of cemented carbide anvil and cylinder is about 1000 times, domestic hard alloy The molds are far apart, and the consumption of hard alloys for synthetic diamonds at home and abroad is shown in Table 2. Table 2 The consumption of hard alloys for synthetic diamond at home and abroad is to expand the high-pressure cavity, changing the situation that we have not produced high-grade diamond for a long time. The sixth grinding wheel factory first introduced the high-strength, coarse-grain synthetic diamond synthesis technology and key equipment. After more than two years of commissioning and batch testing, it was completed in 1990. The imported 50MN synthetic press has the international advanced level in the mid-1980s. It is the most advanced synthetic device in China. After the production, the annual output of synthetic diamond can reach 1.1 million carats. Among them, high grade diamond is 330,000 carats.
LX-650 diamond six-face hydraulic press sixth wheel factory has used the imported synthesis equipment to mass produce four high-grade products of MND12, SMD, SMD25 and SMD30. The quality of the product conforms to the new national standard GB6406-86, reaching the SDA of De Beers Co. , SDA85 and SDA100 product levels. Unfortunately, the problem of localization of large-diameter carbide anvils and cylinders has not been solved, and it is difficult to play its due role. The average life of cemented carbide anvils of 60~70mm diameter of GECo in the United States is more than 3,000 times, and the pressure cylinder is more than 1500 times. The sixth wheel factory introduced a 60mm diameter cylinder from West Germany with an average service life of 1000 times, an anvil of 2000 times, an annual ring mold with an average service life of more than 6000 times per ring, and De Beers Co currently uses a pressure of 110mm. The average life of the cylinder is more than 1000 times, and the anvil is more than 2000 times. The wire winding method adopted by artificial crystals in China starts from the small mold of Ø20mm cavity, and gradually enlarges Ø32mm, Ø40mm, Ø50mm, Ø65mm large molds, and has developed more than 100 sets. It has been used for several decades without breaking accidents. Mature, this technology exceeds the level of similar foreign products. Taking the YX-50 mold as an example, the high pressure chamber volume is 100 cm3. In 1991, 9 (unmodified) were used, and the average life was 121.78. In 1992, 50 cylinders (improved) were used throughout the year, with an average life of 537.86. In 1993, 93 pressure cylinders were used (improved), with an average life of 566.6. In 1994, 100 top anvils were used throughout the year, with an average life of 811.1 times and a maximum life of 7,000 times. In December, 6 pressure cylinders were used (after improvement), with an average life of 609.33 times and a maximum life of 1,500 times.
The hard alloy top hammer Zhengzhou Sanmao and the Jinan Foundry and Forging Machinery Research Institute cooperated closely. In 1964, the design of the DS-023A hinged six-sided anvil ultra-high pressure device was started. It was completed and manufactured in August 1965. The birth of the first 6×6MN DS-023A ultra-high pressure high-temperature device in China has created a new situation in the development of superhard materials in China, and has made significant contributions to the formation, development and growth of the super-hard materials industry. The device has undergone a difficult exploration process from the input process test to the normal operation. There are two outstanding technical difficulties: one is the high-pressure sealing problem; the other is the service life of the cemented carbide anvil, which is proposed through repeated practice: (1) The larger the cone half angle, the greater the strength; (2) The compressive stress on the maximum cross-sectional area of ​​the anvil is 980~1078MPa; (3) The ratio of the top surface area to the maximum cross-sectional area of ​​the anvil is 1:10; 4) The ratio of the length of the top surface of the top anvil to the side length of the cube-leaf stone block is 1:1.4~1.5: (5) The chamfer of the top anvil is generally 40° or 41°; (6) the length of the chamfered side and the top of the anvil The length ratio of the side of the face is about 1:2, etc., as the parameters of the geometry and size of the anvil are correctly selected, thereby solving the above two technical problems. In order to provide ample production space for the production of coarse-grained and high-strength diamonds, the idea of ​​large-scale high-pressure chambers was proposed. From 1966 to 1973, 6×15MN, 6×35MN, and 6×50MN hinged six-sided anvils were designed and manufactured. Ultra high pressure device. However, since the manufacturing technology of large-diameter cemented carbide has not been solved in China, the above-mentioned large-scale apparatus has not been put into operation. In order to adapt to the development of China's synthetic diamond industry, Zhuzhou Cemented Carbide Factory began research work on the anvil for the anvil and the anvil for the four-sided anvil device in 1961. The material of the anvil has been tested with G2, G4 and G6. , G6X; pressure cylinder material used YG15, later changed to YG13. Because YG6X required fine grain tungsten carbide production process is difficult to control, low output is difficult to solve the contradiction between supply and demand of cemented carbide anvil at that time, for this, Zhuzhou hard The alloy plant conducted a comprehensive study on the production of tungsten carbide particles, components and manufacturing processes for the anvil. In 1971, the top anvil for the YG8 six-sided anvil device and the top anvil for the YG4 two-face anvil device were successfully developed. The service life of the YG8 six-sided anvil device reached and exceeded that of the YG6X anvil, which solved the problem of the shortage of fine-grained tungsten carbide and made great progress for the development of synthetic diamond. An important contribution. Reviewing the continual development of ultra-high-pressure devices for superhard materials synthesis in China, it is easy to see that expanding high-pressure chambers, improving product yield and quality, reducing costs, and introducing anvils and pressure cylinders for annual ring-type 50MN high-pressure two-face anvil devices The key to localization lies in the large-scale production of the pressure cylinder and the anvil. Therefore, it must be solved as a major problem. It is understood that Zhuzhou Cemented Carbide Plant has successfully produced Ø270×142mm large-scale two-faced top pressure cylinder (single weight 75kg) and its supporting anvil (single weight 19kg), which was produced by the Institute of Artificial Crystals, through industrial tests. Xianyang Superhard Material Equipment Co., Ltd. cooperated with Zhuzhou Cemented Carbide Factory. On the 400mm 12mn hinged six-face anvil device with cylinder head, Ø105mm carbide anvil (single weight 8kg) was successfully used for high-grade synthetic diamond test. The production technology management efficiency has increased greatly, which has added a strength to the fierce competition of China's synthetic diamond products to participate in the international market. This fact proves once again that the large-scale carbide anvil (pressure cylinder) is of great significance for the technological advancement of superhard material production in China.
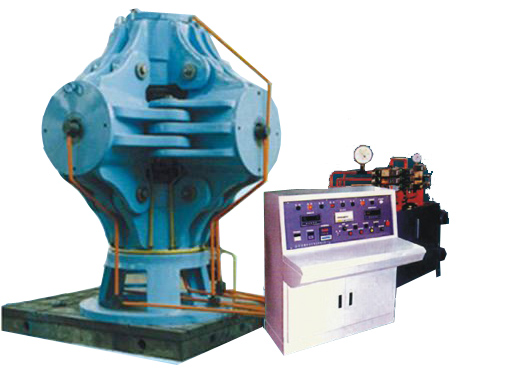
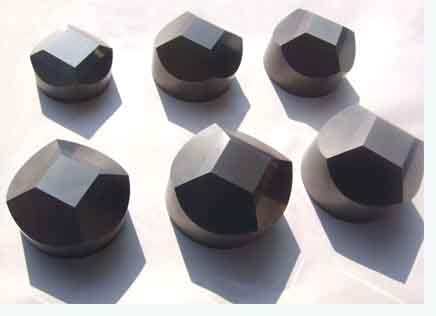
Pipe Stands,Copper Pipe Crimping Tool ,French Drain System ,Pipe Installation Tools
Welding Equipment Co., Ltd. , http://www.nbpowertools.com