TANDEM double wire gas shielded welding is a highly efficient, high speed, adaptable and energy efficient welding process. Compared with ordinary gas shielded welding, the welding efficiency is 3-6 times that of them. When the plate is welded, the deposition rate can reach 30kg/h. The low-alloy high-strength steel required to control the line energy in welding is the best process to replace the submerged arc welding.
0 Preface
With the continuous development of China's shipbuilding industry, shipbuilding output has increased substantially, and the ship type built by shipyards has been increasing. The trend of shipbuilding steel has also changed quietly: the demand for low-alloy high-strength steel will increase substantially. The specification of steel plates for shipbuilding is increased, which will increase the difficulty of the automation panels. First of all, due to the large-scale ship, the demand for low-alloy high-strength steel has increased dramatically. Because ordinary shipbuilding steel has low strength, it is necessary to increase the thickness of the ship when constructing a large ship. This not only increases the difficulty and cost of processing and welding in the manufacturing process, but also increases the ship's own weight and reduces the load; secondly, the large-scale ship has led to the trend of large-scale shipboard specifications. It is expected that the largest marine steel plate specifications will reach: 22.5 m long Width 4.5 m 40 mm thick. The problem of efficient welding of low-alloy high-strength steel and plate is also a problem that every shipyard welding department must face.
In recent years, domestic shipbuilding companies have introduced a number of plane segmentation lines, which have played a major role in the production of shipyards. The plane segmentation line is mainly used for the butt welding of the hull parallel intermediate and outer plates, the double bottom plate, the top plate, the deck partition, and the like, and the welding of the corresponding structure. However, for various reasons, from the current flat pipelines introduced by several major shipyards in China, there are few successes. First of all, the welding materials must rely on imports. Since the equipments introduced are all large-scale and efficient equipment, they are all technical techniques such as high-speed energy high-speed welding. Although some domestic welding consumables can be used instead of imported for the introduction of equipment, the requirements for toughness indicators are high or the welding consumables for special occasions are still mainly imported; secondly, because the equipments introduced are all large-line energy technology, this It is not suitable for the welding of high-strength steel, the heat input is large, and the deformation and the structural properties are caused. The FCB single-side welding plate welding station in the plane segmentation line introduced by many domestic shipyards has a poor gap consistency due to the groove root retention. Such problems lead to uneven forming of the reverse side of the weld, sometimes not even forming, increasing the amount of repair work. Some properties of welded joints of steel plates with thickness ≥ 35mm are not satisfactory. As a result, in some cases the pipeline does not flow, or the flow is not smooth.
1 Introduction to TANDEM Double Wire Welding System
In order to improve the welding production efficiency and welding technology level of China's industrial enterprises, Zhuhai Jinbao Hot Melt Welding Technology Co., Ltd. introduced TANDEM double wire high-speed and high-efficiency welding technology from the world famous German CLOOS company. Successfully solved the needs of some users who need high-speed welding. Over the past ten years, more than 150 sets of TANDEM welding systems have been delivered in China, which has been well received by users.
This technology places two wires in a specially designed torch at a certain angle. The two wires are powered by their respective power supplies. All parameters can be independent of each other, so that the arc can be optimally controlled. Compared with other double wire welding technology, it not only can improve the welding speed, greatly improve the welding efficiency, but also improve the weld quality and reduce spatter.
(1) Principle of TANDEM welding system:
The principle of TANDEM welding system of CLOOS in Germany is shown in Figure 1.
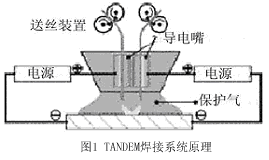
(2) Process characteristics of TANDEM double wire welding:
a) High-performance welding machine, welding current 1000A at 100% duty cycle, pulse current 1500A;
b) Digital dual-pulse power supply, 6-inch LCD display, programmable, connected to PC, printer;
c) The specification parameters of each wire can be set separately, the material and diameter can be different, and the phase difference can be continuously adjusted;
d) The wire feeding speed of each wire can reach 35m / min;
e) Greatly improve the deposition efficiency and welding speed;
f) Maintaining a lower heat input as the deposition efficiency increases;
g) The arc is stable and the droplet transfer is controlled;
h) Small welding deformation;
I) Small splash;
j) Welding data monitoring and management, error code display;
k) Use standard gas, low air consumption;
l) Weldable steel, high strength steel, stainless steel, aluminum alloy, etc.;
2 Shipyard segmentation board technical requirements
The technical requirements for the shipyard segmentation panel are as follows:
(1) One-time welding of 20-40mm thick steel plate, single-sided welding on both sides, the reverse surface is beautiful, and the weld can meet the requirements of ship inspection;
(2) No opening without thickness of 16mm (including 16mm);
(3) Welding speed: 1m/min or more with a thickness of 20mm and 1.2m-1.5m/min with a thickness of 16mm;
(4) It can also be applied to high-speed welding of low-alloy high-strength steel;
(5) Welding deformation control requires no correction after welding;
(6) Can be used with copper pads or ceramic pads;
(7) The group gap precision is allowed to have an error of 2 mm.
3 TANDEM double wire welding panel system
(1) Machine assembly: It includes main gantry, ladder, and lateral sliding mechanism. The main gantry adopts a fixed form and has a length of 21m. It is suitable for plates of different specifications of 21m and below. The welding trolley runs on the gantry beam and has a long welding distance.
(2) Welding assembly: Welding trolley, three-dimensional, up and down lifting mechanism, left and right adjustment mechanism, welding gun clamping mechanism, etc.
a) Welding trolley: adopts bilateral variable frequency drive type, the driving power is 1.5KW, and the welding speed is 300-3000mm/min.
b) Welding gun up and down lifting device: The welding gun carriage is driven by the linear guide rail under the transmission of the precision screw rod. The driving power is: 0.75KW, the moving distance is 500mm, and the speed is: 250mm/min.
c) Left and right traverse device of welding torch: The welding gun is manually moved left and right under the driving of the welding arm, and guided by the linear guide rail, the moving distance is 500mm.
(3) Welding system: It includes two sets of TANDEM double wire welding machine (four sets), four wire feeders, two TANDEM twin wire welding torches and welding torch cables, connecting cables and so on.
(4) Tracking system: Includes laser tracking system and electric cross slide. The cross-slide structure is adopted, and the non-contact sensing workpiece is docked. According to the collected weld change signal, the welding torch is accurately followed by the XY slider, and the precision is ±0.25 mm.
(5) Welding fume Dust Collector: Contains 1 set of German welding fume recovery system.
(6) Arc guide assembly: It includes a welding gun angle adjustment mechanism and a welding gun spacing adjustment mechanism.
(7) Energy transmission assembly: Includes 15000mm long tank chain and roller table. The diameter of the roller is: 245 x 16 mm.
(8) Control assembly: Includes control box, operation box, cable, etc. The control system adopts centralized control, which can store welding process parameters and can be called at any time according to different process parameters.
(9) Steel plate fixing device: Contains electromagnets, etc. Each electromagnet has a diameter of φ250 mm and a suction force of 2 tons. The lateral electromagnet has a pitch of 925 mm and a longitudinal direction of 965 mm. A support roller is arranged in the middle of each electromagnet to facilitate the transportation of the steel plate.
(10) Pad: Includes ceramic or piano copper pads. The ceramic pad is manually attached, and the key pad is padded with a balloon top.
4 TANDEM double wire welding jigsaw welding process:
(1) The two cut steel plates are placed on the roller table for spot welding, and the clearance precision is controlled below 3mm;
(2) The steel plate splice weld is sent to the weld patch through the synchronous conveyor chain, and the ceramic pad or the top lift copper pad is attached on the reverse side to ensure that the back pad is tightly bonded to the weld;
(3) The high-speed TANDEM double-wire gas shielded welder was started for welding, and the two TANDEM twin-wire welding guns were working at the same time. The front gun with a weld seam laser tracking system is used for bottoming, and the rear gun is equipped with an arc swing cover surface for one welding.
(4) Remove the ceramic liner on the reverse side, manually clean the roots and complete the assembly process.
(5) The spliced ​​steel plate is transported to the longitudinal keel assembly area, the longitudinal keel position line is drawn on the steel plate, the keel is assembled and spot welded, and the assembled workpiece is sent from the conveying roller to the longitudinal keel welding zone for double-sided automatic welding.
5 welding parameters <br>The welding parameters are shown in Table 1.
Specimen | Q235 | Welding wire | ER70S Φ1.6mm | ||||
Groove form | Butt weld V-type 20+20mm | Counter gap | 4-5mm | ||||
Welding gas | 80% Ar+20% CO2 | pre-heat temperature | no | ||||
Weld sequence | Bottom TANDEM welding torch | Cover TANDEM welding torch | |||||
Welding wire | Front wire | Back wire | Front wire | Back wire | |||
Welding current A | 260 | 300 | 420 | 380 | |||
Arc voltage V | 28 | 30 | 32 | 31 | |||
Wire feeding speed m/min | 7.0 | 7.5 | 10.0 | 8.5 | |||
Pulse frequency Hz | 200 | 200 | 200 | 200 | |||
Peak voltage A | 32 | 34 | 36 | 35 | |||
Base current A | 100/100 | 100/100 | 100/100 | 100/100 | |||
Pulse waveform | 2 | 2 | 2 | 2 | |||
Pulse width ms | 1.90 | 1.90 | 2.25 | 2.25 | |||
Pulse mode | U/I | U/I | U/I | U/I | |||
Gas flow rate l/min | 25 | 25 | 25 | 25 | |||
Welding speed mm/min | 1000 | ||||||
Swing frequency Hz | 20 | ||||||
Swing amplitude mm | 5 | ||||||
Residence time s | 0.2 | ||||||
Weld width mm | Reverse 6-8 | Front 21-24 | |||||
Remarks: welder related parameter settings: |
Wheel Loader,Construction Equipment,Construction Machinery
Hengxing Industry Machinery Co., Ltd. , http://www.fjconcreteplant.com