With the improvement of the push-to-weight ratio of high-performance aeroengines, the role of the supercharged drum is becoming more and more important. The typical features are complex structure and thin wall thickness, which are prone to deformation during machining, affecting the machining accuracy and processing quality. Affect the performance of the engine. Titanium alloys are widely used in aerospace engines due to their significant strength, corrosion resistance, high temperature and high strength. In this paper, the aero-engine supercharged drum is used as the carrier. According to the characteristics of titanium alloy material and drum structure, by optimizing the process design process, the deformation of the thin-wall drum is controlled to ensure the processing quality of the product.
1. Processing characteristics of titanium alloy materials
Titanium alloy is a typical difficult-to-machine material, and its processing difficulty mainly comes from two aspects: one is determined by the characteristics of the titanium alloy material itself, and the other is determined by the structural characteristics of the part. The characteristics of the titanium alloy material determine its processing difficulties: 1 low thermal conductivity, resulting in poor heat dissipation during the cutting process, resulting in a significant increase in the temperature of the cutting edge of the tool, which seriously affects the tool life and the surface quality of the part. 2The modulus of elasticity is small, and it is easy to produce elastic deformation under the action of cutting force. Strong wear and tear with the machined surface, resulting in increased tool wear and easy to cause cutting chatter. 3 high chemical activity, easy to produce affinity with the tool material, leading to bonding, diffusion, greatly reducing tool life. 4 Titanium alloy material has low plasticity, small chip deformation coefficient during cutting, and high chip flow speed, so the unit cutting force is large, which is easy to cause tool wear.
The structural characteristics of the parts (see Figure 1) increase the processing difficulty. This is because: 1 The supercharged drum is an integral part of the multi-stage gutter. The diameter is generally more than 800mm, the height is about 400mm, and the wall thickness is 2.15mm. Diameter thin wall drum. Due to the poor rigidity of the parts, cutting vibration is easy to occur during processing. On the one hand, the cutting efficiency is seriously affected, and on the other hand, the quality of the machined surface is greatly affected. 2 The pressurized stage drum ring dovetail groove is a closed profile and the cavity is large and small. During processing, the cutting fluid is difficult to spray to the tip of the tool tip, which affects the cooling and lubricating effect and easily leads to heat concentration. 3 Due to the thin-wall structure of the supercharged drum, it is easy to produce the knife during the machining process. At the same time, with the release of residual stress, the processing deformation phenomenon is serious, which affects the machining accuracy of the part.
Figure 1 supercharged drum structure
2. Analysis of the cause of deformation
There are many reasons that affect the deformation of the supercharged drum. However, in the manufacturing system, the main factors of deformation are: the clamping conditions of the parts, the machining residual stress, the cutting force, the cutting heat and the cutting vibration.
(1) Mounting of parts Due to the poor rigidity of the thin-walled parts, improper selection of the clamping force and the supporting force may cause additional stress.
Since the elastic deformation of the clamping will affect the dimensional accuracy and shape and positional accuracy of the surface, and the machining deformation occurs, the clamping and positioning design during the machining of the part is one of the important factors for reducing the deformation and ensuring the quality.
(2) Residual stress parts During the machining process, due to the combined action of the tool on the machined surface, the rake face of the tool and the chip, the friction between the flank face and the machined surface, new parts are created inside the surface of the part. Processing residual stress. The residual stress is an unstable stress state. When the part is subjected to an external force, the external force interacts with the residual stress, causing some of its parts to be plastically deformed, and the stress in the section is redistributed. When the external force is removed, the entire part is internally The effect of residual stress is deformed, and the deformation of the part caused by the redistribution of residual stress during the cutting process has an important influence on the processing quality.
(3) Cutting force and cutting heat In the cutting process, in order to overcome the elastic deformation, plastic deformation of the material to be processed and the friction between the tool and the chip and the workpiece, cutting force and cutting heat are generated, in the cutting force and the cutting heat. Under the action, it is easy to generate vibration and deformation, which affects the processing quality of parts. In addition, the rigidity of the machine tool and tooling, the cutting tool and its angle, the cutting parameters and the cooling and cooling of the parts also have a certain influence on the deformation of the parts. Among all the factors, cutting force, clamping force and residual stress are the main factors that cause machining deformation.
3. Process design
The material of the supercharged drum is Titanium alloy Tc4, and the wool is a die forging. The supplied state is the refined wool after roughing, as shown in Figure 2.
Figure 2 supercharged drum wool
Due to the limitation of ultrasonic flaw detection, the wool profile is relatively simple, and the final profile of the part is more complicated, which makes the machining allowance of each surface have a large difference. Therefore, the rough machining process must be arranged to remove the margin and keep the machining allowance of each surface basic. Evenly. After the roughing, the stress-relieving heat treatment is arranged to remove the residual stress caused by the roughing; after the heat treatment, the parts are deformed. For this reason, the reference process is arranged before the finishing to improve the positioning surface precision of the parts finishing, and the parts are avoided. Deformation caused by error recombination. The main machining process route: machining ultrasonic surface → ultrasonic flaw detection → rough interior and exterior profile → stress relief heat treatment → vehicle benchmark → fine car interior and exterior profile → milling blade installation groove, locking groove → inspection.
4. Deformation control
For the characteristics of titanium alloy materials and parts, comprehensively consider the parts clamping, cutting tools, cutting parameters and path of the tool to control the deformation of the parts.
(1) Fixture structure design Select the matching surface with good rigidity of the part as the positioning surface, adopt the axial positioning, compaction and keep the position of the action point consistent, to avoid deformation of the part under the action of clamping force.
For the structural characteristics of high overall height, thin wall thickness and poor rigidity, when the small end of the part is machined, the end face is selected as the axial positioning support, and the positioning block is radially positioned; when the inner cavity profile is processed, the large size is adopted. When the outer surface is machined, the end surface gland is pressed tightly. When processing the small end faces, considering the high overall height of the parts, the vibration is easy to be generated during processing, so the fixture is positioned. The face is selected at the end face of the middle part of the part, so that the relative height of the positioning surface is lowered, and the overall rigidity of the part can be improved.
Due to the large and thin structural features of the part, as much as possible, the margin is removed as much as possible in the roughing process. However, as the margin is continuously removed, the wall thickness of the part is reduced, and the rigidity is reduced, which causes machining vibration on the surface of the part. The grain is deformed while the part is processed. Therefore, when machining the inner and outer profiles of the parts, the auxiliary support is added to the corresponding parts of the inner and outer profiles of the jig, as shown in Fig. 3, not only increases the rigidity, but also suppresses the machining deformation of the parts, and absorbs the vibration energy of the parts to eliminate the vibration. Improve the vibration resistance of the entire part.
Figure 3 Internal and external profile auxiliary support
(2) Tool material and geometric parameters One of the key factors for the difficulty of machining titanium alloy is the "heat" problem, and the heat of cutting is one of the factors that cause the deformation of the part. When cutting titanium alloy, the chips are easily bonded and welded near the cutting edge of the blade, or a built-up edge is formed, and a high temperature zone is formed on the front and back knives near the entire cutting edge, so that the red hardness of the tool is lost and the wear is intensified. In addition, due to the high affinity of titanium alloys, the tool materials used in the processing of titanium alloys are less titanium or titanium-free. The chemical reaction and welding phenomenon between TiN and TiC in the coated tool and the processed titanium alloy are prone to severe wear, increased cutting force and deformation of the part. To this end, we chose a non-coated ultra-fine grained tungsten-cobalt carbide turning tool with a low affinity to titanium alloy, and the high cobalt type tool is most effective. The main role of cobalt can enhance the secondary hardening effect, improve the hardness of the thermosetting and heat treatment, and at the same time have high toughness, wear resistance and good heat dissipation.
The titanium alloy has a small elastic modulus and a large processing deformation. The back angle of the tool should be larger, generally take αo = 15 ° ~ 18 °, reduce the friction between the machined surface and the flank to improve tool life. When turning thin-walled parts, the front angle should also be larger γo = 10°, and the main declination angle is 75° to 90°, which is beneficial to reduce the radial force and prevent vibration. The radius of the cutter head determines the strength of the tool tip, heat dissipation and wear, and is not easy to be too large. Generally, rε=1~2mm is taken.
Cutting titanium alloys must keep the tool sharp, reduce machining distortion, reduce work hardening, and improve the quality of the machined surface.
(3) Cutting amount The vibration during cutting is one of the important factors that restrict the quality of thin-wall drum processing. It must be guaranteed to process under stable conditions to maximize tool life and ensure machine accuracy. In the optimization of titanium alloy processing parameters, the dynamic characteristics of machine tools, tools and parts must be considered, and the process parameters optimization based on cutting stability is carried out.
The performance of the titanium alloy material determines that when the titanium alloy is processed under the same cutting amount, the cutting force per unit area of ​​the tool is much larger than that of the general steel, and the cutting temperature is much higher, so the tool wears quickly. The machinability of the material deteriorates. In order to improve the cutting conditions, a large amount of soluble cutting fluid is used during processing to reduce the cutting temperature, improve tool life and reduce part deformation. When using a titanium alloy drum, the cutting amount should be v=50~70m/min, f=0.1~0.2mm/r, ap=0.3~1mm.
Selection criteria for the amount of titanium alloy to be cut: a lower cutting speed and a larger feed rate should be used from the viewpoint of lowering the cutting temperature. Due to the high cutting temperature, the titanium alloy absorbs oxygen and hydrogen from the atmosphere, causing the surface of the workpiece to be hard and brittle, causing the tool to wear and wear, causing deformation of the part. Therefore, during the processing, the temperature of the tool tip should be kept at a suitable temperature to avoid excessive temperature and affect the deformation of the part.
(4) Path and path of the cutter The path of the cutter has an important influence on improving the machining accuracy of the thin-wall drum. In the arrangement of the path, first remove the larger surface, then remove the smaller surface in turn, and finally repair the reference surface. For the surface with positioning function, the inner and outer walking method is adopted as much as possible to form a concave microstructure, which is favorable for positioning.
The part with large roughing allowance adopts the inserting layered circulation method, which can effectively improve the processing efficiency and reduce the cutting deformation and its influence, as shown in Figure 4; the finishing process adopts the combination of cycle and contour cutter. Reduce part deformation, as shown in Figure 5.
When cutting the knife, try to make the cutting force of the blade pressed against the direction of the shank to make the machining process smooth; use the relative and opposite traversing method to offset the machining stress, so as to facilitate the uniform removal of the material, make the residual stress uniform release and maintain the rigidity of the part. The balance is to reduce the deformation of the part, as shown in Figure 6.
Figure 4 Internal and external profile roughing cutter path
Figure 5: Finishing of the inner and outer profiles
(5) Programming In the NC programming, fully consider the characteristics of the part structure and optimize the motion trajectory. During roughing, the cyclic NC machining program is programmed to remove the residual amount, which not only reduces the machining stress, but also controls the deformation of the parts, and is beneficial to chip removal and chip breaking, effectively improving the processing quality and processing efficiency of the parts. In the finishing process, the combination of the die-center programming and the contour programming is adopted, and the tangential arc cutting and cutting-out method is adopted in the contour-joining part, so that the cutting and cutting cuts smoothly, and the blade marks are not left on the contour surface, thereby ensuring The surface quality of the part.
Figure 6 knife path
(6) Heat-treated stress-relieving thin-walled parts are easily deformed due to stress release during processing. The process is often carried out by roughing and finishing, and subjected to stress-relieving heat treatment after roughing to remove forgings and roughing. Residual stress. For high-precision parts with severe deformation, semi-finishing is also arranged and multiple stress relief treatments are performed.
Gabion Mesh made of double twisted wire with hexagonal mesh are in accordance with the European norms regarding the quality conditions necessary for the production and usage of gabions: EN 10223-3: 2013 - Hexagonal steel wire mesh products and EN 10244: 2009 - Non-ferrous metallic coatings on steel wire. The wire`s stretch resistance is of 380-550 N/mm2, and the mesh has a stretch resistance of minimum 50 kN/m, according to the requirements of norm EN 10223-3.
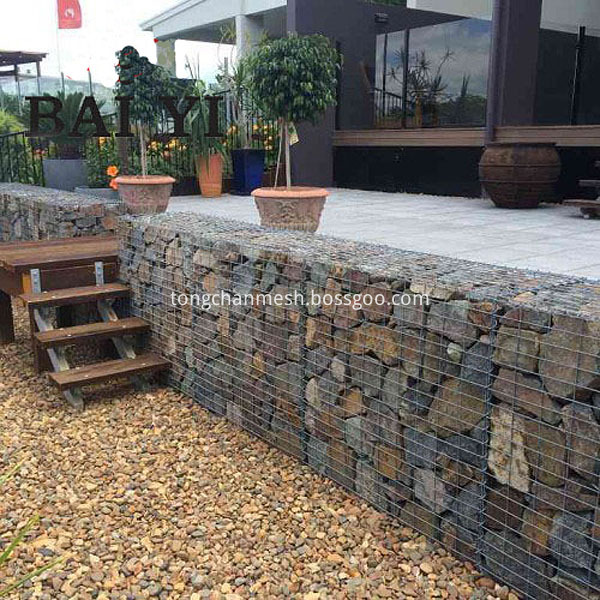
Gabion Mesh
Gabion Mesh,Gabion Wire Mesh,Hexagonal Wire Mesh,Gabion Fence
Hebei TongChan Imp.&Exp.Co., Ltd. , http://www.tongchanmesh.com