(1) The possible reasons for the tool not being able to break the knife include:
(1) The tool holder fails to clamp the tool properly. This could be due to low spring pressure in the clamping jaws, a loose nut behind the spring, an overly heavy tool, or a malfunctioning robotic locking mechanism.
(2) After clamping, the tool cannot be loosened. This may happen if the loosening spring is too tight, preventing the claw from retracting. To resolve this, adjust the nut so that the maximum load does not exceed the rated capacity.
(3) During tool exchange, the tool may be lost. This can occur if the spindle does not return to the correct tool change position, or if the robot grabs the tool off-center and starts pulling it before it's fully positioned. In such cases, move the headstock back to the tool change point and reset the position.
(2) The robot fails to extend and pull the tool out of the spindle and tool magazine. Possible causes include:
(1) A faulty "loose knife" sensor switch. During the tool change process, each action must be confirmed by the sensor before proceeding. If the third step—spindle loosening—is not signaled, the robot will not attempt to pull the tool. Check both sensor switches to ensure they are functioning correctly.
(2) A malfunctioning "loose knife" solenoid valve. The spindle loosening is controlled by the solenoid valve, which activates the hydraulic cylinder. If the solenoid valve fails, the hydraulic cylinder won't engage, and the tool won't loosen. Verify that the solenoid valve operates as expected.
Common Fault Analysis of Robots
(3) The "loose knife" hydraulic cylinder might not operate due to insufficient system pressure, oil leakage, or incorrect stroke positioning. Inspect the hydraulic cylinder, confirm its movement is normal, and check that the stroke is properly aligned. Open the rear cover of the spindle (as shown in Figure 8-2) and verify that the hydraulic cylinder has reached the correct position, with normal oil pressure and no leaks.
(4) Issues within the manipulator system may prevent the "pull the knife" condition from being established. This could stem from a problem in the motor control circuit. Ensure that the motor control system is functioning correctly.
(5) Problems in the spindle system may also cause failure. As illustrated in Figure 8-2, the spindle uses a disc spring, pull rod, and spring chuck to grip the tool shank. When the tool is loosened, the hydraulic cylinder’s piston presses the ejector rod, which pushes the pull rod through a hollow screw. This motion allows the spring chuck to release the tool’s pull stud, enabling it to move rightward and become "loose" inside the spindle taper.
(3) The spindle system may fail to loosen the tool for several reasons:
(1) The tool pull pin is too short, causing the hydraulic cylinder to move into place without actually loosening the tool.
(2) The position of the hollow screw at the end of the tie rod has shifted, leading to inadequate stroke for the "loose knife" function.
(3) The ejector rod is damaged or worn, affecting its ability to push the pull rod effectively.
(4) The spring chuck is faulty and unable to open properly.
(5) During assembly, the tool movement was adjusted too minimally, resulting in insufficient loosening during operation.
Approach:
Remove the "loose knife" hydraulic cylinder and inspect the adjustment of the cannulated screw during assembly. It was found that the stroke was correct, but the extrusion on the tool shank inside the spindle taper hole was insufficient. Adjust the "extension amount" of the cannulated screw to ensure that after the hydraulic cylinder stroke is complete, the shank is extruded by 0.4–0.5 mm. After this adjustment, the issue was resolved.
Conclusion
As cutting speeds increase and machining times decrease, the demand for faster tool changes continues to rise. Tool change speed has become a key performance indicator for high-end machining centers. While automatic tool changers are reliable and accurate, their complex structure makes increasing speed technically challenging. Modern high-speed machining centers from advanced manufacturers incorporate fast automatic tool changers to meet these demands, often using innovative technologies and methods.
The technical level of functional components, their performance, and overall industry support directly influence the capabilities of CNC machine tools and affect the development of the mainframe. The tool changer plays a critical role in ensuring stable and reliable machining center operation. Its fast and precise tool change program significantly impacts the efficiency and reliability of the machining process. Without a tool changer, a centralized process machining center would not be feasible. According to data, about 25% of machine failures are related to the tool magazine and robot [1]. Therefore, the performance and quality of the tool changer directly impact the performance, quality, and variety of CNC machines.
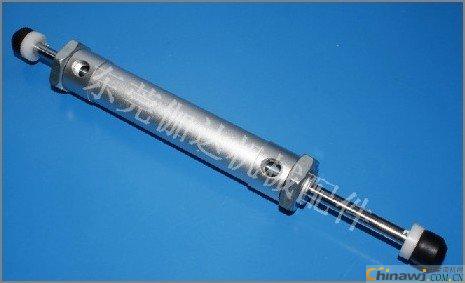
Aluminum Awning Windows: Combining Style with Practicality
Welcome to the world of Aluminum Awning Windows, where modern design seamlessly meets functional versatility. Crafted with precision engineering and durable materials, these windows offer a perfect blend of sleek aesthetics and practical benefits. Let's explore the features and advantages that make Aluminum Awning Windows an ideal choice for contemporary homes and commercial spaces.
Contemporary Design:
Aluminum Awning Windows feature a sleek and contemporary design that adds a touch of sophistication to any architectural style. With clean lines and slim profiles, these windows offer a minimalist aesthetic that complements modern building designs.
Effortless Operation:
Designed for ease of use, Aluminum Awning Windows open outward from the bottom with the help of a crank handle. This unique operation allows for ventilation even during light rain, making them an ideal choice for areas where protection from the elements is essential.
Customization Options:
We understand that every project is unique, which is why we offer a range of customization options for Aluminum Awning Windows. From frame finishes to glass types and hardware styles, you can personalize your windows to match your architectural vision and design aesthetic.
Experience Modern Luxury:
Upgrade your space with the sophistication and functionality of Aluminum Awning Windows. Contact us today to explore our range of products and discover how Aluminum Awning Windows can elevate the aesthetics and performance of your home or commercial building.
Aluminum Awning Window,Triple Glazed Windows,Basement Awning Window,Aluminum Awning Window Shades
Foshan City JBD Home Building Material Co.,Ltd. , https://www.jbdhome.com