(1) The possible reasons for the tool failing to release the knife are as follows:
(1) The tool holder does not securely clamp the knife. This could be due to insufficient spring pressure in the clamping jaws, a loose nut behind the spring, an overly heavy tool, or a malfunctioning robotic locking mechanism.
(2) After clamping, the tool cannot be loosened. This may happen if the loosening spring is too tight, preventing the jaws from retracting. To fix this, loosen the nut so that the maximum load remains within the rated limit.
(3) During tool exchange, the tool might be lost. This can occur if the spindle housing does not return to the correct tool change position or if the position has shifted. Additionally, if the robot grabs the tool but it's not properly aligned, pulling the tool out prematurely can cause it to be lost. In such cases, the headstock should be returned to the tool change position, and the position should be reset.
(2) The robot fails to extend the tool and pull it out from the spindle and tool magazine. Possible causes include:
(1) A failure in the "loose knife" sensor switch. During the tool change process, each action relies on signals from sensor switches. If the signal is not received, the next step will not proceed. For instance, after the third step—spindle loosening—the robot will not attempt to pull the knife. Check both sensor switches to ensure they are functioning correctly.
(2) A faulty "loose knife" solenoid valve. The spindle loosening function is controlled by the solenoid valve, which activates the hydraulic cylinder. If the solenoid valve fails, the hydraulic cylinder won’t engage, and the tool won’t loosen. Ensure the solenoid valve is operating normally.
Common Fault Analysis of Robots
(3) The "loose knife" hydraulic cylinder may not operate due to low system pressure, oil leakage, or incorrect stroke positioning. Inspect the hydraulic cylinder to confirm it’s working properly and that the stroke is accurate. Open the rear cover of the spindle (as shown in Figure 8-2), check the hydraulic cylinder, and confirm it has reached the correct position with normal oil pressure and no leaks.
(4) There may be an issue with the manipulator system, preventing the "pull the knife" condition from being met. This could involve a problem with the motor control circuit. Verify that the motor control system is functioning correctly.
(5) Issues within the spindle system may also cause the problem. As illustrated in Figure 8-2, the spindle uses a disc spring, pull rod, and spring chuck to hold the tool shank. When the tool is loosened, the hydraulic cylinder pushes the ejector rod, which then moves the pull rod through a hollow screw. This action loosens the spring chuck, allowing the tool to move rightward and become "loose" inside the spindle taper hole.
(3) The likely reasons why the spindle system isn't loosening the tool include:
(1) The tool pull pin is too short, causing the hydraulic cylinder to reach its position without fully loosening the tool.
(2) The hollow screw at the end of the tie rod has shifted, resulting in an insufficient stroke for the "loose knife" operation.
(3) The ejector is damaged or worn, affecting its ability to push the pull rod.
(4) The spring chuck is faulty and cannot open properly.
(5) During assembly, the tool movement was adjusted too little, leading to issues during use that prevent the "loose knife" condition from being met.
Approach:
After removing the "loose knife" hydraulic cylinder, the issue was traced back to improper adjustment of the cannulated screw during assembly. As a result, even though the hydraulic cylinder stroke was correct, the tool wasn’t extruded enough to be removed. Adjusting the extension amount of the cannulated screw ensured that the tool shank was extruded by 0.4–0.5 mm into the spindle taper hole after the hydraulic cylinder stroke was complete. After this adjustment, the fault was resolved.
Conclusion
With increasing cutting speeds and shorter machining times, the demand for faster tool changes is growing. Tool change speed has become a key performance indicator for high-end machining centers. Although automatic tool changers are reliable and precise, their complex structure makes it technically challenging to increase the speed. Advanced foreign machine tool manufacturers now equip high-speed machining centers with fast automatic tool changers to meet these demands, often using new technologies and methods.
The technical level of functional components, their performance, and the overall support system directly influence the performance and development of CNC machines. The tool changer is essential for the stable and reliable operation of a machining center. Its fast and accurate tool change program plays a crucial role in the efficiency and reliability of the machining process. Without a tool changer, a centralized process machining center would not be feasible. According to data, about 25% of total machine failures are related to the tool magazine and robot [1]. Therefore, the performance and quality of the tool changer significantly impact the performance, quality, and variety of CNC machines.
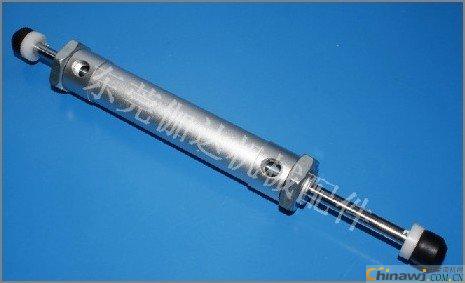
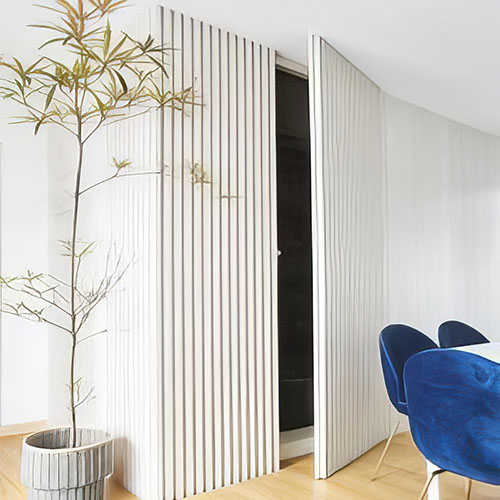
An interior invisible door is a very unique door design that blends seamlessly with the surrounding wall, making the presence of the door almost invisible when closed. This type of door design is not only designed for visual simplicity and aesthetics, but also for practicality. Despite their simple appearance, invisible Doors retain the functionality of traditional doors, including smooth opening and closing, as well as good sound and thermal insulation.
Interior invisible doors have several functions:
1. Space-saving: Invisible doors are flush with the wall when closed, saving space in a room compared to traditional swing doors that require clearance for opening.
2. Seamless design: Invisible doors blend seamlessly with the wall, creating a clean and minimalist look in a room without interrupting the overall design aesthetic.
3. Increased privacy: Invisible doors can provide privacy in spaces such as bedrooms, bathrooms, or home offices without the need for a visible door handle or hardware.
4. Improved accessibility: Invisible doors can be used in areas where traditional swing doors may not be practical, such as tight spaces or areas with limited clearance.
5. Noise reduction: Invisible doors can help reduce noise transmission between rooms, providing a quieter and more peaceful environment.
Overall, interior invisible doors offer a sleek and functional solution for modern interior design, providing a seamless and space-saving alternative to traditional swing doors.
solid wooden doors,Invisible door,Concealed Sliding Door
Foshan City JBD Home Building Material Co.,Ltd. , https://www.jbdhome.com