Abstract In recent years, the development of science and technology has led to the development of processing materials for enterprises, while cutters, plain bearings, tensile dies and various wear parts are usually made of cemented carbide. As the processing strength continues to increase, cemented carbide tools are also exposed to wear resistance and toughness in applications...
In recent years, the development of science and technology has led to the development of processing materials, and tools, sliding bearings, tensile dies and various wear parts are usually made of cemented carbide. As the processing strength continues to increase, cemented carbide tools also expose soft ribs that do not compromise both wear resistance and toughness in applications. In order to meet the requirements of high efficiency, high precision and high reliability of modern machining, it is necessary to further improve the comprehensive cutting ability of tool materials. The processing industry also urgently needs to reform and innovate tool products and develop new high-efficiency, long-life products to promote the prosperity of its market. Through previous research, it is found that the main development direction of cemented carbide tools and related problems are:
(1) Refinement of crystal grains to increase the surface area and bonding force between hard phases, thereby improving the strength and wear resistance of the material, but due to the immaturity of the refining process and the high price of fine-grained hard alloys, Affects tool quality and limits its application;
(2) Perform surface heat treatment to change the composition and structure of the binder phase in the material to achieve the purpose of improving strength and toughness, or to perform cyclic heat treatment on the whole to alleviate or eliminate the stress between grain boundaries, but the method has comprehensive performance. The improvement is not obvious;
(3) Strengthening the hard phase structure, that is, by appropriately adding rare metals or rare earth metals, the chip performance can be further improved;
(4) Coated cemented carbide, coated with a thin layer of wear-resistant materials (such as TiC, TiAlN, Al2O3, diamond, etc.) by CVD, PVD, HVOF, etc., combined with high strength, high toughness and coating of the substrate The advantages of high hardness and high wear resistance reduce the friction factor between the tool and the workpiece, and improve the wear resistance of the tool without reducing the toughness of the substrate. Therefore, coated cemented carbide has high hardness and excellent wear resistance, prolonging the life of the tool, which is a great revolution in the development of cutting tools.
Diamond is the hardest substance in nature, with special properties such as low wear resistance, high thermal conductivity and excellent chemical stability, making it an ideal material for abrasives and cutting tools. However, the use of diamond alone is brittle and cannot be processed with high strength, and the single crystal diamond tool is limited in its application field due to high cost and poor impact resistance. And the performance is similar, but the cheap diamond film has more room for development. When selecting a tool for machining, it is usually desirable to have a high hardness to ensure good wear resistance and high toughness to prevent chipping, and the combination of cemented carbide and CVD diamond film can meet the requirements. This requirement makes the tool exhibit both high hardness and wear resistance of the diamond, as well as good impact resistance and toughness of the cemented carbide itself, and low manufacturing cost, which makes it extremely powerful in the field of machining. Application market.
The data shows that the diamond coating can greatly improve the performance of cemented carbide tools, such as non-ferrous metals and their alloys, composite materials, ceramic materials, etc., the service life can be increased by dozens of times [5]. Using CVD In the method, the prepared diamond film contains less impurities, and the growth is easy to control, especially for a base material having a complicated geometric shape, which can be deposited well. Commonly used CVD methods include hot filament CVD, microwave plasma CVD, and direct current plasma CVD. At present, CVD diamond coating technology has become more and more mature. There are many companies in the world that have developed and produced CVD diamond coated tool technology, such as: sp3 of USA, Diamond Coating Tool, Cemecon of Germany, Balzers of Switzerland, OSG of Japan. Wait. CVD diamond coated tools will be widely used in ultra-precision machining, such as automotive, aerospace, integrated circuit boards. China has gradually become a superpower of processing materials, and the demand for tools is also huge, but the research on CVD diamond coating tools is still far from the foreign countries.
Research on CVD Diamond Coating Tool Technology
Since the researchers in the laboratory of the ASEA (Allmanna Svenska Elektriska Aktiebolaget) in Sweden successfully produced the first diamond in 1950, the researchers have been working on the development of various new diamond tools (Fig. 1), and gradually have many excellent diamonds. The nature of the application to various fields. In the process of developing the tool, the original natural diamond was used as the cutting tool. In 1977, GE successfully developed the diamond sintered body (PCD) tool instead of the natural diamond tool, followed by the synthesis of large particles of single crystal diamond. In order to replace the natural diamond, the development of CVD technology has pushed diamond tools from thin film to thick film. Driven by the market, diamond tools are also facing new high performance with high strength, long life and low cost. Material transformation. After more than 20 years of development, CVD diamond coating has overcome various technical problems, mainly to ensure the following two key points: one is to ensure the quality of CVD diamond film on the cemented carbide substrate; the other is to ensure the diamond film and lining The strength of the bond between the bottoms.
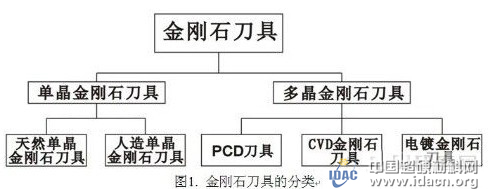
Method for preparing CVD diamond coating
As the tool market continues to evolve, it is necessary to explain the preparation of CVD diamond coated tools. Chemical vapor deposition (CVD) is a method of decomposing gaseous raw materials (such as methane and hydrogen) under high temperature to form active particles such as carbon atoms or methyl radicals, and depositing a diamond film on the surface of the substrate under certain process conditions. method. The main methods are different according to the form of the excitation plasma: hot wire chemical vapor deposition (HFCVD), microwave plasma chemical vapor deposition (MPCVD) and DC Arc Plasma Jet.
At present, the hot wire CVD method is the most common and mature method for preparing diamond coated tools. Due to the low cost and high controllability of the hot wire method, it is the main method in industrial applications, and foreign tool companies have also developed Production of deposition equipment. As shown in Fig. 2(a), Model 650 (currently Model 700) developed by sp3 company has a hot wire CVD coating device with a large deposition area (Fig. b), which enables high-efficiency product output. In Figure 2, c and d are the hot wire devices of Cemecon and Diamond Coating Tool respectively.
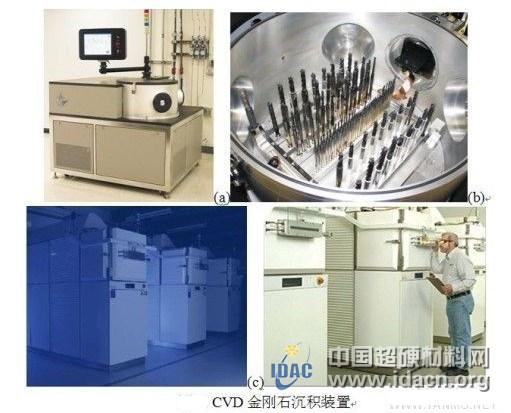
Effect of Co on cemented carbide substrates
It is well known that WC-Co cemented carbide is mainly composed of refractory metal compound particles of tungsten carbide and metal binder phase cobalt. The presence of Co also gives the matrix itself good toughness and flexural strength. According to the percentage contained in Co, it is divided into different models: YG3 (the mass percentage of cobalt contained is 3%), YG6, YG8, YG10, YG13, YG15, and the like. However, the presence of Co will affect the diamond deposition process. This is due to the high solid solubility of Co in the cemented carbide relative to carbon, which greatly slows the nucleation process of diamond, and Co, like other transition metals, grows in the film. The process has the effect of promoting the conversion of diamond to graphite (non-diamond carbon), which will also greatly reduce the adhesion of the diamond film.
The existence of metal bonded phase Co is also one of the key points of research. If the content of Co in cemented carbide is low, it will be beneficial to the deposition of diamond film, but its toughness will not be used as a high-strength processing tool. . The alloy tool with high Co content is the best tool body material, but the disadvantage of Co to diamond film is the bottleneck that its high performance is difficult to play. Therefore, this contradiction has also prompted researchers to find ways to eliminate and reduce the adverse effects of Co. But the most important thing is to find the most suitable cobalt-containing carbide substrate, which can meet the compressive strength of the cemented carbide substrate and reduce the impact on diamond growth.
Initially, the researchers tried to reduce the unfavorable factor by removing the surface Co, that is, pretreating the surface of the cemented carbide and removing the Co on the surface by acid etching, which is beneficial to the nucleation of the diamond on the surface of the alloy. However, carbon has high diffusivity and permeability in Co, which leads to the deposition of Co at the surface temperature of 700 ° C to 900 ° C. The Co of the inner layer diffuses to the surface with a concentration gradient, thus forming a surface layer. The diamond reacts to form a non-diamond phase that affects the bonding force of the film.
In order to study the relationship between the Co content in the alloy and the quality of the diamond film, Wei Qiuping studied the cemented carbides YG3, YG6, YG10 and YG13 with different contents of Co, and deposited the diamond film by pretreatment with acid etching. Hard alloys with low Co content can not only better deposit diamond films, but also the toughness of cemented carbides. Such cemented carbides with small Co content have also been the focus of research.
At present, domestic attempts are also being made to prepare gradient cemented carbides, so that the growth problem can be more effectively overcome by adding WC grains. This technology has been commercialized abroad for a long time. Sweden's Sandvik Company has introduced DP (D1Properties) series of gradient carbide ball teeth with GC215, GC425 and other coated cemented carbide ladder blades: GTE.alenite, USA KV792M coated coated carbide inserts from SV200 series and Kennametal; WC grain gradient carbide top hammers from Boart, Ireland. These products have been widely used for their superior performance.
Improve the deposition quality of diamond film by improving the process
A key technology for the preparation of CVD diamond coated tools is to improve the quality of the diamond film, which is closely related to the control of CVD technology and process parameters (such as gas source ratio, substrate temperature, working pressure, working time, etc.). . Since the deposition process is carried out on a heterogeneous substrate, coupled with the etching action of Co on the diamond, nucleation is difficult, and it is desirable to enhance the nucleation of the diamond by various methods. As shown in Table 2, the nucleation density of the diamond on the cemented carbide substrate was enhanced by various methods, and a certain effect was achieved.
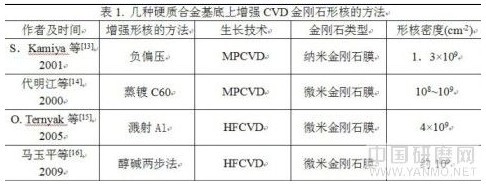
At the same time, during the growth of diamond film, the control and improvement of process parameters also affect the quality of diamond. Generally, the gas source for generally growing diamond is a combined gas of H2 and CH4, and XM Meng et al. added Ar gas to the gas source to obtain a smoother and denser nano-diamond film, which is added by the addition of Ar gas. Density and promote the decomposition of H2 and CH4, thereby promoting the growth rate of secondary nucleation and diamond. In addition, the exploration of a good growth environment during the deposition process is also necessary, and the optimal growth parameters of different equipment are also different. Sarangi et al. used HFCVD to deposit diamond films on cemented carbide substrates to study the effect of pressure on growth. It is believed that better surface morphology and strong adhesion can be obtained under moderate working pressure, which will also be more Helps to improve its cutting performance.
Wei Qiuping studied the quality of the deposited diamond film under different air intake modes (Fig. 3a) through the improvement of the equipment. It is considered that the air intake mode directly affects the composition, distribution and density of the atmosphere around the substrate. The nucleation density, crystal morphology and growth texture of the diamond film have a very significant effect. In industrial applications, it is usually necessary to overcome the influence factor of the diamond film deposited on the complex shape of the tool. Xie Peng et al. used the MPCVD method to deposit the PCB bit, and the wire shield (Fig. 3b) was successfully overcome. The impact of the "tip effect." Zhang Xianghui et al. improved the equipment by adding a temperature automatic control system with a substrate to ensure a constant substrate temperature, which contributes to the stable growth of the diamond film. By contrast experiments, deposition on the YG6 alloy is more A dense, flat film. Our laboratory also used microwave plasma CVD to study the effects of methane concentration and produced diamond coated inserts in small batches at low methane concentrations. Therefore, only by constantly adjusting the process and breaking through the old thinking can we explore more novel "points" to improve production efficiency.
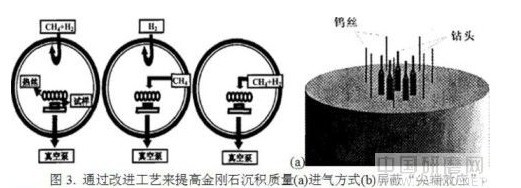
Study on the method of improving the adhesion of film base
The key to the preparation of CVD diamond coated tools is to improve the adhesion between the film and the substrate, and there are two reasons for its adhesion: one is the presence of metal Co in the alloy to promote the conversion of diamond into graphite; the second is because of diamond The thermal expansion coefficient between the film and the cemented carbide substrate is very different, causing the film to collapse when it is lowered to room temperature after the end of growth. Therefore, various methods for improving adhesion are based on these two.
Purification and decobalting treatment of alloy substrate surface
The surface pretreatment process is indispensable before deposition. This is due to the presence of a large amount of contaminants, adsorbates and oxides on the surface of the alloy. The presence of a large amount of impurities on the surface of the substrate will greatly affect the direct contact of the diamond film with the substrate. Furthermore, it is more advantageous to deposit the diamond by removing the surface Co, which is usually effective to enhance the adhesion after pretreatment.
The surface of the substrate is cleaned, ground, polished, and the like to remove various impurities on the surface of the alloy to improve the nucleation rate. Maintaining a clean substrate surface is a prerequisite for obtaining a high-quality diamond film. By ion bombardment, etching, laser treatment, etc., the grain can be refined, the surface roughness and the film base contact product are increased, and the adhesion of the diamond film is improved. Also by subjecting the surface to acid-base treatment, the most classical method is to use Murakami reagent (m(K3[Fe(CN)]6)=10 g, m(KOH)=10 g, V(H2O)=100 mL)) Etching the tungsten carbide phase, then treating the deep cobalt with acid to improve the diamond deposition quality and adhesion. Table 2 lists the common pretreatment methods, but many methods of decobalting treatment can only be applied to low cobalt content. Good results are not achieved in cemented carbides, not in high cobalt content alloys.
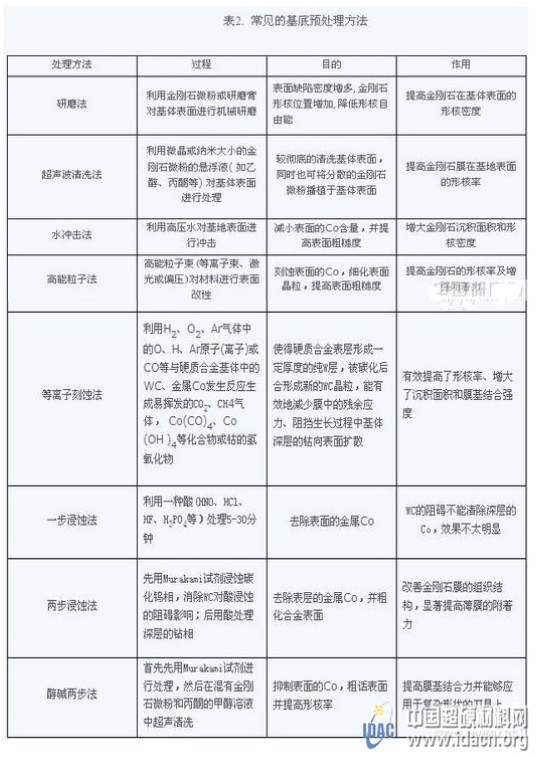
Through various methods of removing surface Co, the effect of Co on the diamond deposition process cannot be completely eliminated, because various methods can only temporarily eliminate the Co phase of the surface layer, and the substrate begins with the deposition process. After the temperature rises, the Co of the inner layer will diffuse again to the surface layer with the concentration gradient, thereby affecting the deposition of diamond. Moreover, there is a large difference in the coefficient of thermal expansion between the diamond and the cemented carbide substrate. When it is lowered to room temperature, there is a high residual stress. Excessive residual stress causes the bonding force between the film and the substrate, and even the film appears. Fall off. Therefore, the method of simply eliminating Co on the surface of the alloy cannot be achieved. At present, the most effective method is to add a transition layer between the substrate and the film. As shown in Fig. 4, the transition layer has good compatibility with the substrate material and the film. After the transition layer is added, the interface will mutually diffuse through the transition layer. Selecting a material with a small thermal expansion coefficient of diamond can not only prevent the diffusion of cobalt on the alloy, but also eliminate the internal thermal stress. Another advantage is that the addition of the transition layer can be deposited on the alloy with high Co content. CVD diamond film, which is more conducive to improve the cutting performance of the entire tool, which is currently the most popular method at home and abroad.
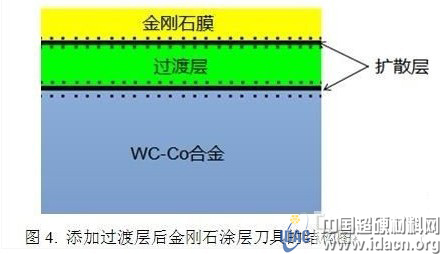
Although the transition layer is beneficial to reduce the influencing factors, the choice of the transition layer material must also meet certain conditions. 1. The intermediate layer material with thermal expansion coefficient between the diamond film and the cemented carbide substrate and close to the diamond film and low elastic modulus, so as to reduce the influence of thermal stress and ensure the adhesion strength; 2. It can ensure the diamond has a high nucleation density and has good bonding properties with diamond and substrate materials. 3. It can form a stable compound with Co to prevent the diffusion of Co to the surface layer and diamond coating at high temperature. Protective layer, the following table. Lists the research on the use of the addition of a transition layer in recent years to improve the deposition of CVD diamond films on cemented carbide surfaces.
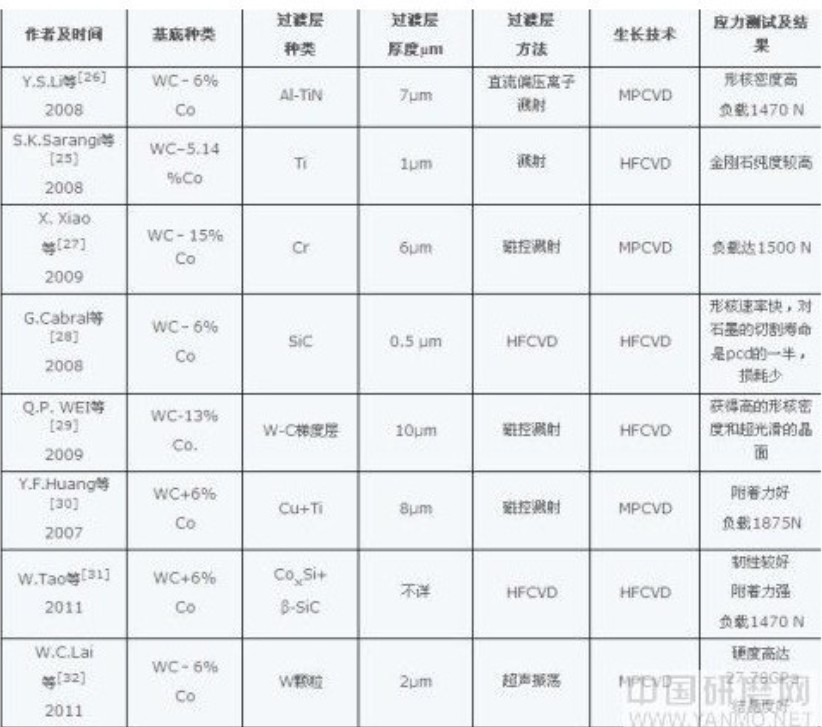
Various methods for preparing the transition layer include a coating method, an electroplating method, an electroless plating method, a vapor deposition method, a magnetron sputtering method, a plasma decarburization method, and a carbonization method. Initially, the transition layer is mainly composed of a single material, such as Ti, W, Cr, and Mo. These elements can form stable compounds with Co and combine with carbon to form strong chemical bonds, which helps solve the problem of diamond adhesion. However, with the deepening of research, a single transition layer can not completely overcome the existing problems, so the multi-layer or composite transition layer has gradually become a research hotspot.
As early as 1999, sp3 applied for a patent on the surface of WC-0.6%Co by adding a WC transition layer to improve adhesion [36], this transition layer can effectively reduce the residual stress in the film, and It can block the diffusion of cobalt from the inner layer to the surface during diamond growth, and the same transition layer and substrate material can greatly improve the adhesion. X.Xiao et al. synthesized nano-diamond films by adding a Cr transition layer on a high-Co content cemented carbide (WC-15%Co) substrate. It is believed that Cr can form a protective layer during diamond deposition to hinder the diffusion of Co. And can form a stable carbide with C, because the diffusion rate of C in Cr will be much smaller than other elements such as Si, Ti, etc., so it will be deposited rapidly in a short deposition time, so that the grain at the interface is relatively Dense, which will improve the adhesion of the diamond to the substrate, greatly improving the processing efficiency of the aluminum alloy.
YSLi et al. first studied the transition layer of Al, TiN and TiCN and found that the Al layer can form a compound with C to improve the nucleation of diamond, while Ti can effectively inhibit the diffusion of metal Co, and then the transition to Al-TiCN. The layer was studied and found to have a nucleation density of up to 5x107 cm-2, and a dense, high-purity diamond was obtained after 12 hours of deposition. Among them, Al element plays a big role. Firstly, Al can effectively inhibit the Fe-based element's role in promoting diamond formation of graphite, so it plays a big role in the diffusion of Co. Secondly, Al film has a higher surface energy and It is chemically active, so it is easier to form Al4C3 at the initial stage of deposition, so that the carbon-aluminum compound contributes to the high nucleation density of the diamond. At the same time, since the carbon aluminum compound also increases the contact area of ​​the base surface and fills the void of the interface, it is more advantageous to enhance the adhesion strength of the diamond film to the substrate. At the same time, Al metal is also a cheap and easy to obtain material compared with the gas metal transition layer material. The application of Al and other elements will be a hot spot in the research of transition layer method. The material laboratory of Hunan University in China studied the Cu transition layer, the Ti transition layer and the Cu/Ti composite coating respectively. It was found that the Cu transition layer can effectively fill the void caused by etching Co on the surface and maintain the strength of the substrate. And surface roughness. When the Ti transition layer is added, C can form a compound TiC similar to the diamond structure with Ti, which is beneficial to the nucleation of the diamond and improves the adhesion between the film bases. Therefore, Cu/Ti is added by combining the advantages of both. The composite coating solves the problem of adhesion and nucleation.
At present, there is still a problem in the preparation of CVD diamond coated tools by adding a transition layer, that is, the preparation process of the transition layer is cumbersome, and even a variety of processes are used, and usually a direct one-step method for the addition of the transition layer cannot be directly performed. And the growth of diamond film, followed by the expensive of the transition layer material, must constantly explore cheap materials for production applications.
6 Hydrogen Peroxide,Hydrogen Peroxide,Food Grade Hydrogen Peroxide,5 Hydrogen Peroxide
Rucheng Sanxing Electric Chemical Co.,Ltd , https://www.3xchemical.com