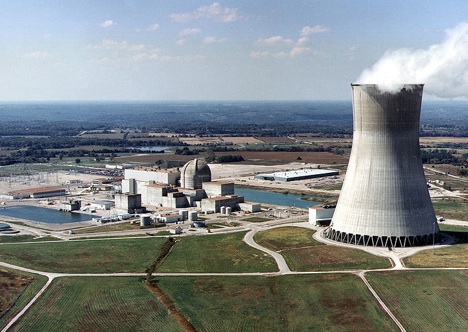
It is reported that this advanced research and development of AP1000 inspection technology with completely independent intellectual property rights has enabled China to get rid of its dependence on foreign AP1000 inspection technology, breaking the technical limitations of foreign countries and effectively protecting the construction and operation of China's third-generation nuclear power projects.
The appraisal experts agreed that the completion of the project enabled China to have independent and independent engineering application technology capabilities in the key technology areas of the AP1000 nuclear power unit in-service inspection. This has provided technical conditions for the safe and efficient operation of the AP1000 nuclear power unit in China, and the overall achievement of project research has been achieved. The international advanced level, among which AP1000 reactor pressure vessel safety tube weld seam ultrasonic inspection technology and many other technologies are original technologies, reaching the international advanced level.
Original innovation leads breakthrough
According to the information provided by CNNC, the 11 key technologies identified through this appraisal include reactor pressure vessel inspection technology, ultrasonic inspection technology for the main end of the pump's safety end weld, reactor control bundle inspection technology, steam generator tube plate flushing, etc. AP1000's key equipment has formed a more comprehensive AP1000 operating technology system for the AP1000 Advanced PWR nuclear power plant.
Among the 11 technologies developed, 5 technologies are dedicated inspection technologies developed for AP1000 units; 6 technologies are based on the inspection technology of M310 units to conduct research and development, which can be used for inspection of AP1000 units and can be used To improve the advanced operation technology of M310 and other units. Moreover, most of the newly developed technologies are original and innovative technologies.
According to reports, through the research on the 11 key technologies of the AP1000 in-service inspection, combined with existing technologies, China has already possessed all in-service inspection capabilities required to implement AP1000 reactor regulations. This technology is expected to be put into use next year in the AP1000 world's first project - the three-door nuclear power project.
The reporter learned that the successful R&D of the AP1000 in-service inspection technology has laid the foundation for the development of other three generations of nuclear power reactors. The mastery of AP1000 in-service inspection technology is like entering the “threshold†of third-generation technology and facing different situations. The heap modelling only requires partial targeted research and development, and research and development work has begun on other three generations of reactor types. Progress has been relatively smooth.
According to industry insiders, the most important achievement in more than ten years of R&D history is the original innovation capability in the technical field where it is located. With original innovation capabilities, it is possible to get rid of the “wealth of foreigners must have†climbing and catching up, and then to achieve the “self-research and development status†of “we can have no foreign countriesâ€.
San Bao Nuclear Power Safety Operation
It is understood that AP1000, as the third generation of advanced nuclear power technology introduced by China's Westinghouse Electric Company, may become one of the major reactor types for China's future nuclear power construction. The three units 1, 2 and Haiyang 1, 2 currently under construction are the first AP1000 units in the world. The first unit is expected to be put into operation in 2014.
The data shows that the structure and size of key equipment such as reactor pressure vessels, steam generators, main pumps, and main pipelines of the AP1000 unit are quite different from those of existing domestic M310 and VVER reactors. Some equipments use a unique structure, such as an integrated top cover for pressure vessels, direct installation of the main pump under the steam generator, etc. The size of the evaporator is greatly increased and the heat transfer tubes are arranged in a triangular arrangement. The structural uniqueness requires the redevelopment of new in-service inspection and inspection technologies.
In order to ensure the smooth operation of the unit, and safe, reliable and economical operation during the lifetime, it is necessary to master the AP1000 operating technology and have the full operational capability of China's autonomous implementation of the AP1000 requirements. During the operation of the unit (including the period of shutdown and refueling), The crew provides regular technical services in operation. Under the support of China National Nuclear Corporation’s priority development of key technology projects, CNNC Nuclear Power Operation Research Institute and CNNC Wuhan Nuclear Power Operation Technology Co., Ltd. have launched the AP1000 in-service inspection of key technologies for scientific research since 2008.
It is reported that all project research has been completed, the research process meets the requirements of the “Quality Insurance Outlineâ€, and a full range of test tests have been completed in accordance with the requirements of the “Test Outlineâ€. The test results meet the requirements of the technical specifications.
Aluminum Auto die casting parts/ truck parts
Description:
Passive one does not use any mechanical components and the heat can be dissipated through convection or transferred through liquid or gas caused by molecular motion.Our aluminum heat sink is used to absorb thermal energy or heat from another object through thermal compounds which are also known as thermally conductive materials. At a relatively high temperature, the heat is absorbed from the object and transferred to the heat sink which has a much larger heat capacity. Being a practical thermal energy solution for both low and high volumes, extruded aluminum heat sink is widely applied for heat radiation of refrigerators, engines, medical devices, lasers, cpus, etc. These applications are quite helpful in such industries as electronics, medical equipment, industrial manufacturing, household appliance, led lighting, and military industry, etc.
Our advantages:
In-house tool / mould making, mould design team , In- house die cast, Assembly line
Exporting Experiences.
Aluminum die casting Auto parts
Protection Board,Aluminum Die Casting Auto Parts,Die Board,Die Casting Bolts
Dongguan Hongge Hardware Technology Co., Ltd , http://www.honggecasting.com